Precision cutting, drilling, milling of micro components
Enter a world where detail and high-tech sophistication converge.
Precision cutting, drilling and milling of micro components application overview
Navigating the world of micro-component precision cutting and milling is a high-tech challenge. Defining a balance between sharp tolerances and diverse material complexities is crucial. Despite tool wear and heat-induced complications, maintaining quality and efficiency remains paramount. As the industry evolves, so too must the techniques, ensuring that micromachining innovation always meets precision.
Precision we can achieve
In the domain of precision cutting, drilling, and milling, the complex process of handling micro components is key to achieve harsch requirements - e.g. achieving machining geometries as small as 20 micrometers and maintaining a precise ratio of up to 1/10 for diameter to depth. This attention to detail ensures high positioning accuracy. Turning operations take pride in delivering an exceptional surface roughness, narrowing down to 50 nm.
You currently have a precision cutting, drilling and milling of micro-components project and you would like to know what we could achieve together?
Give us some more details
The FEMTOsecond LASER technology is a perfect match for all industries requiring the highest precision without compromising quality and productivity.
Miniaturized components are used in all kind of devices. Several applications – e.g. in the electronics or MedTech world – are not imaginable without very small and tiny parts. Thus, this requires new ways to produce and manufacture these parts. With FEMTO LASER μ-machining there are various processes possible like drilling, cutting and turning. It's compatible with almost all materials that are otherwise very difficult to machine with conventional tools.
With each FEMTOsecond LASER pulse that hits the work-piece, a small amount of material immediately vaporizes. The material removal occurs in a controlled manner leading to no damage, burrs or any negative influences to the material integrity.
Your benefits:
- FEMTOsecond Laser source < 300 fs
- Highest level of accuracy and productivity
- Stable and repeatable quality
- Cold ablation keeping material integrity (no HAZ)
- Proven performance in 24/7 industrial environment
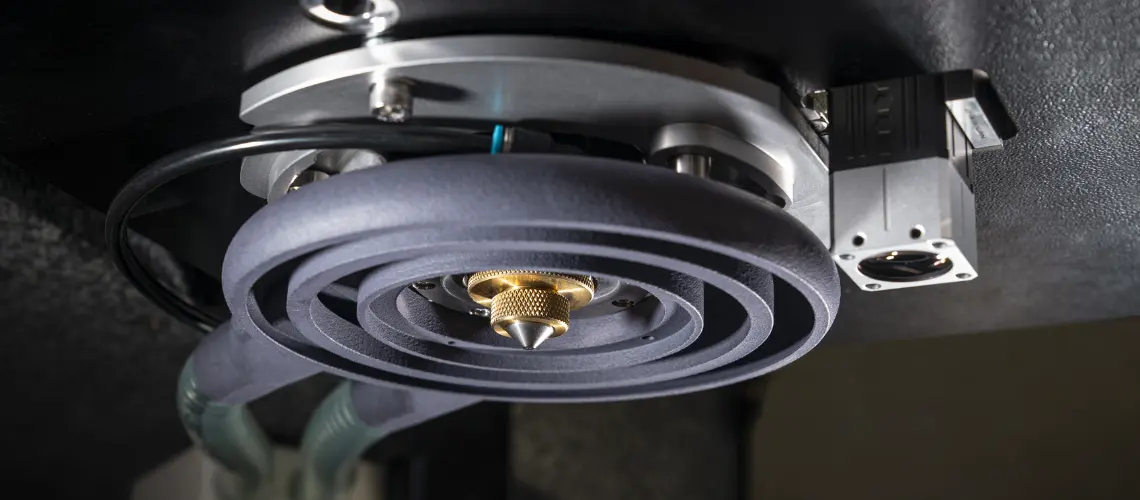
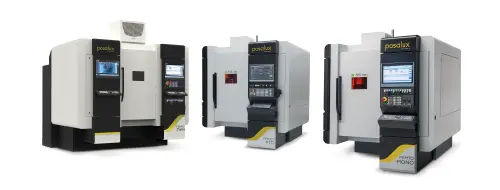
FEMTOsecond LASER machines provide advanced µ-machining solutions for high-tech production. It ensures impeccable surface smoothness and precise machining without thermal residue.
Other applications that might be interesting for you
Gear cutting operations for the watchmaking industry
Let’s discuss your micro-machining operations
If you are looking for a high-tech production system as well as a partner to process state-of-the-art micro-machining, you are in the right place.